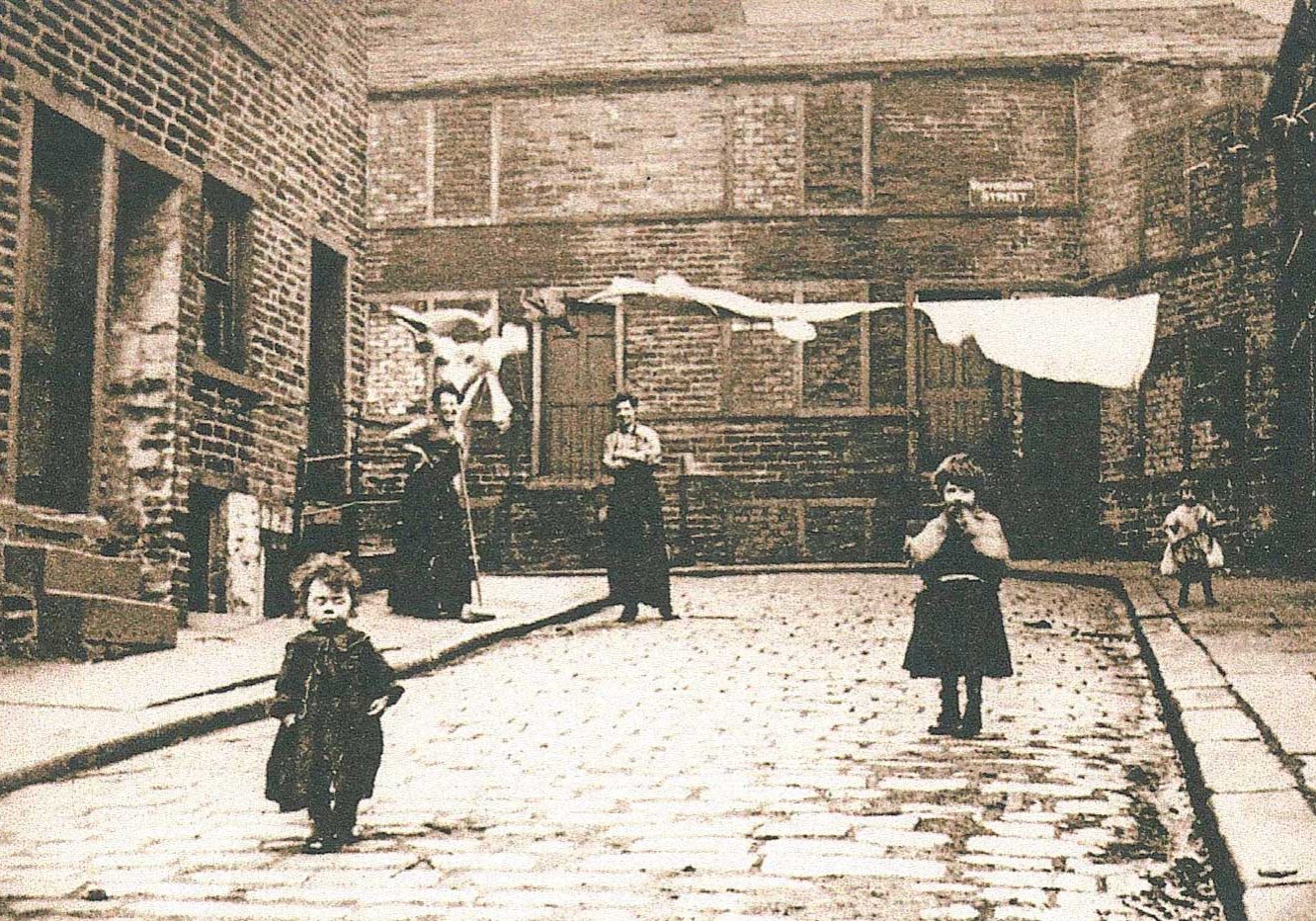

Bradford at Work: People and Industries Through the Years
by Northern Life
The Wool Capital of the World
£12 BUY NOW
The Bradford economy owes as much to its pre-eminence as an international textile hub as it does to iron and steel. Bradford’s textile industry can be dated back to the thirteenth century, but 1825 was a pivotal year. That was the year when the wool-combers union called a strike that lasted five months; workers were eventually forced back to work through penury and the much-dreaded introduction of machine-combing went ahead. This local industrial revolution ushered in a period of rapid growth, with wool imported in prodigious quantities for the manufacture of worsted cloth. Worsted was a fine wool fabric used in top-end clothing and refers to a type of yarn and the fabric produced by this yarn. There are two principal types of wool warn: woollen and worsted, using fleeces from different breeds of sheep that are prepared and spun differently. Worsted uses fleeces that have long fibres using combing machines to ensure the wool fibres like parallel to each other and are of the same length. This produces a smooth, strong yarn. In woollen yarn, the fibres are shorter, of varying length, and point in all directions; they are fluffy and uneven.
Worsted yarn produces fabrics that are durable and have a fine, smooth texture while woollen products are softer and warmer. Worsted yarn is used in clothing such as men’s suits and woollen yarns are more suitable for knitwear and blankets. Bradford earned the sobriquet ‘Worstedopolis’.

Two fourteen-year-old workers at the mill in 1930, namely Lilian Marsden and her friend Phyllis. Lilian is carrying a hook on the string round her waist, which was used to wind the yarn onto the spinning frame
In 1800, Bradford’s population was 13,000 and it had just one spinning mill. By 1850, the population had grown to 103,000, while the number of spinning mills had surged to 129. In 1900, the number of mills had increased further to 350. Two-thirds of the country’s wool production was now processed in Bradford.
Bradford coal kept the mills and other industries in power and local sandstone was mined for building the many mills. By 1875, the population had risen to 182,000 attracting yet more workers to jobs in the textile mills. Local soft water was used in cleaning raw wool but water, or the lack of it, was a seriously restricting problem in Bradford Dale, curbing as it did industrial expansions and the improvement of urban sanitary conditions. So, in 1854 Bradford Corporation bought the Bradford Water Company and initiated a huge engineering programme to deliver soft water from Airedale and Wharfedale. Urban creep took in the Hortons and Bowling, resulting in an interrupted urban and industrial landscape by the late nineteenth century, swallowing up the green fields between each of the communities.
One significant employer was Samuel Lister and his brother who were worsted spinners and
manufacturers at Lister’s Mill, or Manningham Mills. It was the largest silk factory in the world. In its heyday, 11,000 men, women and children were working at Lister’s. Among other things, Lister’s could lay claim to over 200 factory chimneys spewing out toxic black, sulphurous smoke all day long, adding to the regular outbreaks of cholera and typhoid. A shocking statistic – even by the standards of the day – is that only 30 per cent of children born to textile workers reached the age of fifteen. Life expectancy in Bradford was just over eighteen years, one of the lowest in the country.
Child Labour in the Mills
- Child labour – a global problem. This image shows children working in a mill in Macon, Georgia, in 1909
- Poverty in Bradford, soon to be a thing of the past for Salt’s workers
In England and Scotland in 1788, two-thirds of the workers in 143 water-powered cotton mills were children. Children made up a significant proportion of the workforce in Bradford’s textile mills: families relied heavily on the extra income the children brought in. Some parents even sold their children to mill owners. Children often worked up to fourteen hours a day.
Work roles performed by child workers included the following:
- Scavengers were the smallest and youngest members of the workforce. They crawled about collecting fibres of wood that fell under the machine – a hazardous task when you think that the deafening and dangerous machines were still running all the while.
- Lap joiners had to keep the spinning machines constantly fed with wool. They swiftly joined together the end of one wool top and the start of the next wool top. Skin sores were common as a result of this work.
- Piecers joined together, by hand, any threads that were broken during spinning and weaving. Broken ends had to be fixed rapidly to ensure the work continued. Speed and dexterity were essential: piecers could easily walk up to 20 miles a day doing their job.
In a bid to curb this ongoing atrocity the Factory Acts were passed. Children younger than nine were not allowed to work; those aged nine to sixteen could work sixteen hours per day as laid down by the Cotton Mills Act. In 1856, the law allowed children over the age of nine to work sixty hours per week, night or day. In 1901, the permitted child labour age was raised to twelve.
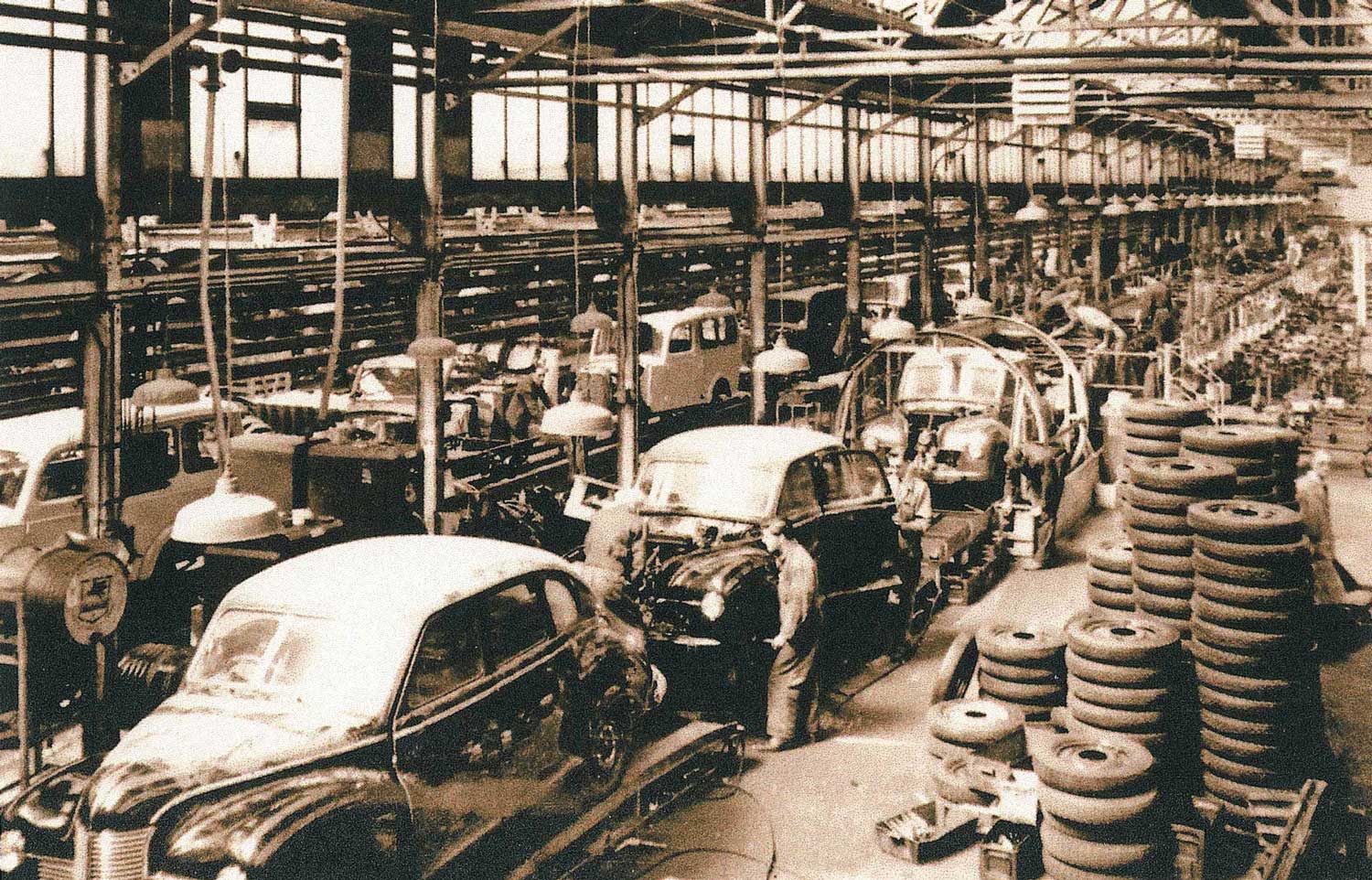
Idle workers on the Javelin assembly line at Jowett Cars Ltd in Idle, near Bradford. The Jowett Javelin was an executive car produced from 1947 to 1953
Bradford: after the revolution (post 1840) and into the twentieth century
The Jowett Motor Company
The Jowett Motor Company was a prestigious motor car company operating from Bradford from 1901-1954, thus spanning the golden age of British motor car production. The company was founded in 1901 by brothers Benjamin and William Jowett together with Arthur V. Lamb.
In the very early days the company focussed on transport of the two-wheeled variety, taking advantage of the contemporary craze for bicycles and cycling. Vtwin engines for driving machinery followed. The first Jowett light car prototype came off the production line in February 1906, however, as the workshop was already busied with general engineering work and manufacturing the first six Scott motorcycles, the inaugural model did not to go into production until 1910. The mission was to offer a low-weight vehicle at a modest price and with low running costs – in effect the United Kingdom’s first real light car.
In the First World War, the factory was converted to a munitions manufacture. After the armistice in 1919, a new site was bought at Springfield Works. The first vehicle to come out of here was the Jowett Seven. Commercial vehicles based on the car chassis were manufactured from 1922 and became an increasingly important part of the company’s portfolio and output.
In 1952, the bottom fell out of the export market. Sales fell by 75 per cent on top of unexciting, sluggish domestic sales. The Jowett Jupiter spots car was still popular and were built up until the end of 1954. Jowett’s sold their factory to International Harvester, tractor builders at the site until the early 1980s.